Understanding OGI Detector Pixel Size
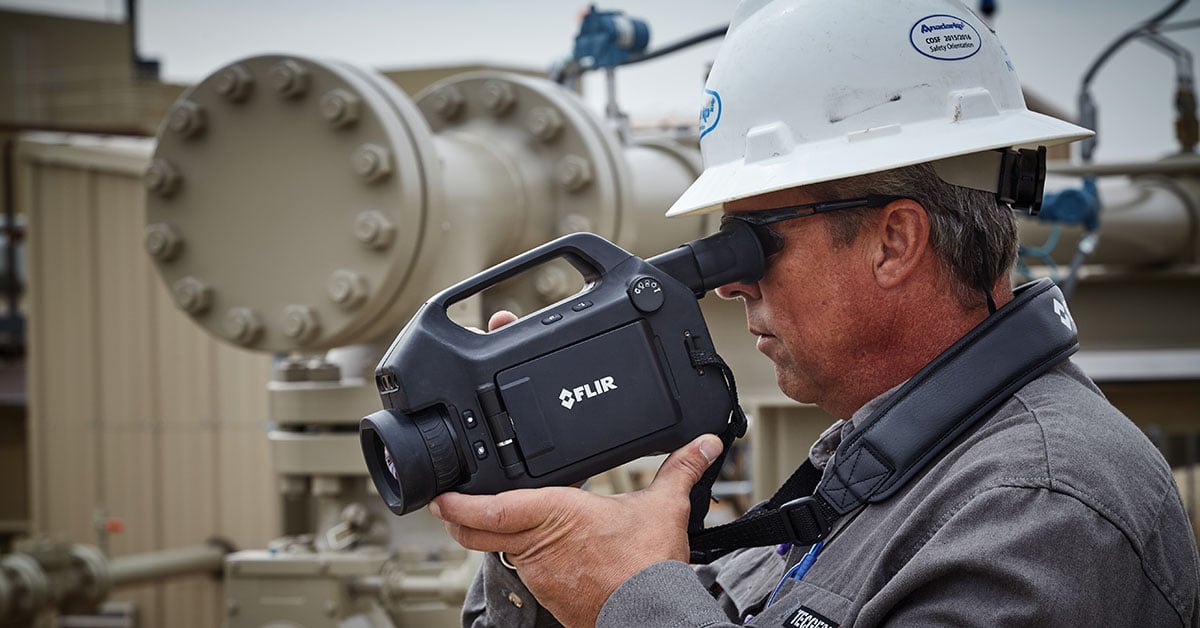
Why Bigger Pixels Can Be Better
While resolution has historically been a key specification when choosing infrared cameras, the choice is not black and white when applied to some oil and gas imaging applications.
By Craig O'Neill, FLIR Systems, Inc.
Chief among specifications, in nearly all types of imaging, is resolution. However, in some optical gas imaging (OGI) applications, it is beneficial to opt for a lower resolution camera to achieve optimal performance.
This article discusses why high resolution is not always king in OGI, notes scenarios in which higher resolution is desired, and introduces FLIR OGI solutions to meet any resolution needs your operation may experience.
Specifications Don’t Tell the Whole Story
Much of the equipment used by oil and gas operators is bought while focusing solely on specifications, with resolution being considered one of the most vital specifications, if not the most important. While this purchasing method is efficient and cost-effective, it also is hazardous in that users of OGI cameras can—deliberately or inadvertently—focus on specifications that may not be key to the equipment’s performance in their specific application.
Great specs are just that: specifications that look appealing on paper. Functionality can be a different thing entirely. It depends on context, most notably application area and budget.
Resolution is at the heart of this discussion. A vendor may claim, "Our camera has X resolution, and our competitor’s camera has lower resolution. Higher resolution is better, so our tender is more attractive.” The argument makes sense; it’s easy to understand and almost universally accepted. Additionally, when choosing an infrared (IR) camera (non OGI), resolution has historically been a key specification to consider. But higher resolution is not always the right choice.
You Say You Want More Resolution, Well, You Know…
OGI cameras operate in the IR wavelength. Thus, it is easy to see where oversimplification could arise because, in most IR applications, adding pixels to a camera will make it “better” because you have smaller spot size ratios (measurable areas) to get more accurate measurements, as well as improved image quality (via greater resolution).
Effective OGI, however, depends on both infrared resolution and gas sensitivity. Sensitivity is measured via noise equivalent concentration length (NECL), which gauges how much gas over a path of a certain length can be detected above the intrinsic noise of the camera.
Several parameters are key to understanding how these two characteristics interact and comprise important camera purchase considerations in their own right:
- Pixel Size
- Pixel Pitch
- Thermal Sensitivity
- Gas Absorbance
1.) Pixel Size—For OGI, resolution and NECL are not linear. In fact, they contradict one another. Consider, as stated earlier, that in non-OGI IR camera applications, the higher the resolution, the better the camera’s ability to diagnose an issue radiometrically (i.e., measuring the target’s surface temperature by interpreting the IR signal intensity reaching the camera). As the pixels get smaller and the object to measure stays the same size, you get more pixels on target and improve measurement accuracy.
In that same vein, consider temperature measurement vs. OGI: In Fig. 1, more “white” appears in a single pixel when the resolution is greater/pixel is smaller. If you average all the area in that pixel (i.e., color), the more white filling the pixel, the more accurate the temperature (intensity) reading. This is a scenario where high resolution is advantageous.
Figure 1
More resolution generally is desirable in OGI applications where one seeks greater leak definition—allowing for identification of more leak details—or when attempting to define small leaks (Fig. 2).
Figure 2
2.) Pixel Pitch—Conversely, in gas detection, users usually are not concerned with the “size” of the pixel compared to the object in view. Gas detection’s greater concern is the amount of energy reaching one pixel; you want as much energy to reach that pixel as possible.
As you add more resolution (more pixels) to a focal plane array (FPA), the size of each pixel (measured in micrometers and referred to as “pixel pitch,” or the space from one pixel center to the next) typically gets smaller in an effort to keep the overall detector size smaller. This reduces the amount of “energy” each pixel gathers and renders the imager less sensitive. In general, these two things contradict each other (resolution goes up, sensitivity goes down). Thus, for OGI, a larger pixel pitch is preferable, as it captures more energy.
For example, among FLIR cooled OGI cameras, the GFx320 camera has a pixel pitch of 30 µm while the GF620 camera has a pitch of 15 µm, making the GFx320 slightly more sensitive than the GF620 (15 mK vs. 20 mK). In terms of NECL, the GF620 NECL for methane is about double the GFx320. While the GF620 remains sensitive enough to meet the most rigorous requirements in sensitivity levels, such as EPA NSPS 40 CFR Part 60, Subpart OOOOa, this may not be the case for all high resolution OGI cameras.
In terms of “small leaks,” a GF620’s higher resolution (640 × 480 versus 320 × 240; see Fig. 2) can provide some advantages. First, you can more clearly see leak definition and potentially learn more details on the leak. You can combine this greater resolution factor with the imager’s digital zoom capabilities to see a much clearer image and, in turn, visualize smaller leaks.
3.) Thermal sensitivity, or noise equivalent temperature difference (NETD), describes the smallest temperature difference you can see with a camera. The lower the number, the better the infrared system’s thermal sensitivity. This measurement is generally taken at an industry standard temperature of 30°C.
If your targets to be measured typically exhibit wide temperature differences, a camera with a low NETD probably isn’t necessary. However, for more subtle applications, like detecting moisture issues, more sensitivity is advisable. In many cases, OGI focuses simply on “is there gas present/escaping or not?” making NETD a less significant factor than, say, pixel pitch.
4.) Gas Absorbance—Without a gas absorbing in the spectral range of the IR camera (filtered or not), the imager will not be able to see the gas. Stated differently, the IR camera’s resolution will not affect the camera’s ability to see the gas if the gas imaged does not absorb energy in the camera’s spectral range.
Figure 3
Additionally, FLIR’s patented High Sensitivity Mode (HSM) has been bolstered with more pixels, which could help with the detection of smaller leaks. This fundamental OGI attribute varies by the gas. Absorbance can be described in terms of a gas’ response factor (RF); the higher the value, the better the gas can be imaged. For example, propane has a higher RF value than methane for cooled cameras (about three times as much) as it absorbs more energy in the filtered IR spectral region in FLIR’s OGI cameras used to visualize hydrocarbon and VOC leaks. (Fig. 3).
Conclusions
While high-resolution imaging may not be the most important factor in all OGI applications, it could be very beneficial in others.
Individuals whose duties include leak detection and repair (LDAR) or service as a health and safety executive (HSE) often are tasked with using OGI cameras to find gas leaks in need of repair, either for maintenance or regulatory compliance. FLIR cameras empower these workers to locate minute leaks and characterize leaks that have been discovered, as well as maintain personnel safety throughout the process.
Whatever your resolution and NECL needs, FLIR offers an OGI camera to serve them, including the GFx320, GF320, GF300, G300a, and GF620, engineered specifically for detection of hydrocarbons and VOC gases.
Ask an expert about ogi cameras