Acoustic Imaging Transforms Refrigerant Leak Detection for Enhanced Safety and Performance Across a Variety of Industries
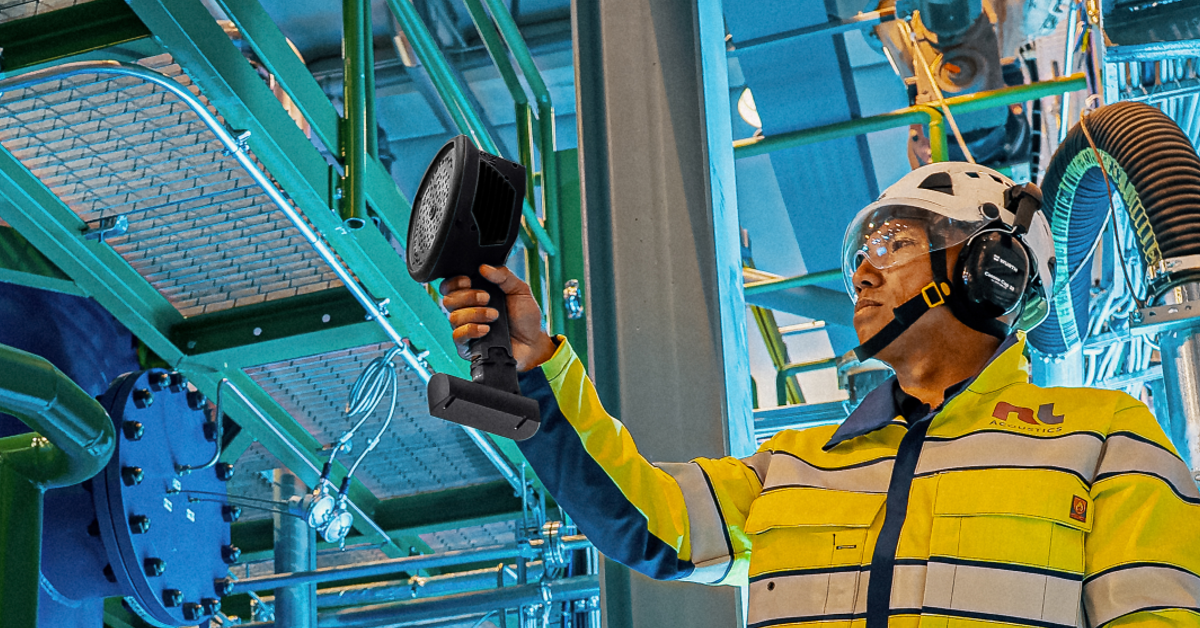
Regular leak detection in refrigerant systems is vital to prevent environmental damage, ensure energy efficiency, and maintain system reliability. Acoustic imaging is highly effective in pinpointing refrigerant leaks, thereby facilitating prompt repairs and minimizing potential safety risks associated with such leaks.
Refrigerant gasses are widely used for many purposes, including heating, ventilation, and air conditioning (HVAC) systems for residential, commercial, and industrial air conditioning applications and automotive air conditioning. They are also vital for refrigeration systems used in various sectors, including the food and beverage industry, pharmaceuticals, chemical storage, and cold chain logistics, as well as certain industrial processes that require cooling or refrigeration, such as chemical manufacturing and petroleum refining. Leaks in refrigerant systems can lead to environmental concerns, energy inefficiency, and potential safety hazards. Many refrigerants, such as R22 (chlorodifluoromethane), have been identified as contributing to the depletion of the Earth’s ozone layer. Other refrigerants, like R32 (difluoromethane) and ammonia, while more environmentally friendly, can still have a negative impact if released into the atmosphere in large quantities. Ammonia leaks can also be hazardous to human health. Detecting leaks in refrigerant systems is therefore critical to protect the environment, improve energy efficiency, maintain system performance, ensure safety, and comply with legal requirements.
FLIR Si124 Acoustic Imaging Camera
Addressing Size, Space, Evaporation, Noise, and Cost Constraints in Refrigerant Leak Detection
The diverse range of applications utilizing refrigerant gasses corresponds with the multitude of industry-specific and often complex challenges caused by leaks. Refrigerant leaks can be very small and difficult to detect, and they often occur in intricate piping networks, connections valves, or even within the equipment itself. Some components of refrigerant systems may be located in confined or hard-to-reach spaces, making it especially challenging to inspect and access potential leak points. Many refrigerants used in HVAC and refrigeration systems are volatile and evaporate quickly, which makes it difficult to detect leaks as the refrigerant may dissipate before it can be detected. The fast evaporation rate requires prompt and efficient leak detection methods. Refrigeration systems also mostly operate in noisy environments, especially in industrial settings. Background noise from machinery, ventilation systems, or other equipment can interfere with leak detection efforts. Implementing leak detection measures, especially in large-scale systems or complex installations, can also be costly and time-consuming, and involve equipment upgrades, retrofitting, or the use of specialized tools and technologies, resulting in further challenges for organizations in terms of resource allocation and downtime during the detection process.
Refrigerant gasses serve diverse purposes in various industries, including their use in gas coolers at oil and gas processing platforms.
Acoustic Solution for Safe and Efficient Operations and Reduced Energy Waste
An acoustic camera is an extremely suitable tool for conducting refrigerant inspections as it detects the characteristic sound emissions produced by minute refrigerant leaks, even in large facilities and surrounded by noisy machinery. The sensitive camera is able to pinpoint leaks quickly and accurately, enabling prompt repairs and enhancing safety for both workers and the environment. The device is easy to operate with minimal training and the inspection method is completely non-disruptive, which saves both time and money by preventing unnecessary downtime due to the dismantling of equipment or halting operations. Through its accompanying analytics software, the acoustic camera delivers actionable data for maintenance and repairs and helps optimize system performance, ensure efficient operation and reduce energy waste, resulting in considerable savings.
FLIR Thermal Studio Suite with the Si-Series Plugin
Benefits of an Acoustic Camera for Refrigerant Leak Detection
• Saves time, energy, and costs by locating hidden refrigerant leaks promptly.
• Enhances production efficiency by preventing unplanned downtime through early leak detection.
• Enables quick scanning in large facilities as well as intricate equipment and hard-to-reach spaces.
• Accurately pinpoints critical problems, even in noisy environments.
• Ensures product quality by preventing defects caused by refrigerant leaks in manufacturing processes.
• Improves operator safety by detecting potentially hazardous ammonia leaks early on.
• Requires minimal training and can be easily integrated into the maintenance cycle.
• Allows for non-disruptive inspections.
• Helps minimize the environmental impact by preventing the release of harmful refrigerants into the air.
• Provides real-time results and actionable data for maintenance and repair plans through AI-driven analytics.
Learn more about FLIR's acoustic imaging solutions at flir.com/si124