FLIR Thermal Imaging Cameras Help To Ensure Consistent Quality of FIAT Cars
Cars need to be light to be efficient in their fuel use, but they also have to be strong. To achieve both of these goals modern car panels are made of a combination of a metal layer on top and a structural adhesive layer underneath. These layers are glued together using induction.
But this is a tricky process. The temperature has to be exactly right for the adhesion to work properly. To ensure that the adhesion goes smoothly FIAT has started to use FLIR thermal imaging cameras to provide automatic feedback during the process.
Each green square in this thermal image stands for one of the measurement spots, 19 in this case. The user can define as many measurement spots as needed.
The flexibility of car exteriors is regulated in stringent safety requirements, to ensure optimal safety for both drivers and pedestrians. Currently the automotive industry preferred method to reach these requirements is a combination of a light metal surface and sophisticated bonding with chemical components to give stiffness to the bonnet on the edges, while maintaining the elasticity at the centre of the bonnet. This helps to keep the car structure rigid, while the car's exterior components remain flexible in order to avoid injuries to pedestrians in case of an accident.
The process of combining these two elements is called bonding. To bond plastic and metal the adhesive needs to be within a temperature range of 150 to 180 degrees Celsius. Modern car manufacturers use a method called electromagnetic induction to reach the required temperature. Using an electromagnet so called 'eddy currents' are generated in an electrically conducting object, in this case the metal layer. The resistance of the metal leads to the generation of heat.
Heating up to 180 °C within seconds
Using conduction the metal layer of the component is heated to the required temperature within mere seconds. The heat of the metallic surface allows the structural adhesive to reach the temperature of pre-polymerization, by going through a viscous to a solid state, bonding with the metal layer in the process.
The time it takes to complete this process differs depending on the type of adhesive used and on the amount of bonded joints required. Usually, it takes approximately 40 to 45 seconds, from start to finish.
But like with all other processes something can go wrong. If for some reason the temperature at one or more adhesion points is not within the temperature range at which the adhesive functions properly, either too high or too low, this leads to weakness in the resulting component.
Quality controls with A-Series camera ensure proper adhesion
FIAT was looking for a method to ensure that the adhesion had worked, while the production process is in full operation. The Italy based company Inprotec delivered just that: a quality test using the FLIR A615 thermal imaging camera.
Inprotec was founded in 1992 in Milan as a distributor of high-tech equipment for industrial safety applications. Soon the professionals of Inprotec realized the potential of thermal imaging technology, so the company became an official FLIR products distributor. Nowadays the Inprotec Group has regional offices not only in Milan, Italy but also in Rome, Sicily, and even in Algeria.
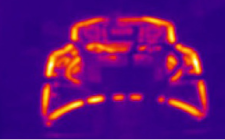
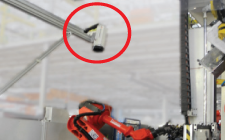
The reliable and accurate FLIR A615 thermal imaging camera detects temperature differences as small as 0.05 degrees Celsius and produces thermal images at a resolution of 640 × 480 pixels. If the induction heating process fails to reach the right temperature an automatic alarm will go off, to warn the operating personnel. Since the bond is unsuccessful if the temperature requirements aren't met, the component has to be discarded if that is the case.
Roberto Ricca, Director of Sales at Inprotec's Thermal Imaging Department is very happy with the quality of the FLIR A615 thermal imaging camera. "It provides exactly the detailed thermal data needed for this type of application."
Software
Using the FLIR Software Development Kit, Inprotec developed the interface for the thermal acquisition of the induction process using the FLIR A615. The thermal data are stored on a server for quality traceability of the production of car bonnet. The technicians at Inprotec inserted the thermal imaging camera in a hard protective exterior and installed a fan that prevents fumes from dirtying the thermal imaging camera's optics. The distance to the measured component is 4 meters, to allow automated robot arm handling during loading and unloading of components. A user friendly touch screen user interface allows quick and easy operation by the plant's personnel.
GigE Ethernet connection
"The thermal imaging camera's fully radiometric video footage is transferred to the computer using a GigE Ethernet connection", continues Ricca. GigE Vision is a new camera interface standard developed using the Gigabit Ethernet communication protocol. GigE is the first standard to allow for fast image transfer using low cost standard cables even over long distances. With GigE Vision, hardware and software from different vendors can interoperate seamlessly.
Marco Simioli, technical manager at KGR, the manufacturer of the induction equipment, is very pleased with the FLIR A615 thermal imaging camera. "With the FLIR A615 system we are able to reach the optimum performance of the production line. The thermal data allows us to evaluate and optimize the heating process. The alarm allows the operators to eliminate the components that do not fit the requirements and to take corrective actions to ensure a perfect production line."
System can be adapted for future use
The computer compares the temperature readings of 16 or more locations with previously determined parameters. If the detected temperature values are too high or too low an alarm will go off. According to Ricca the user can quite easily add extra measurement spots. "This is an important feature. Because this system is flexible it can be adapted for use with future car models as well."
Every new car model includes an increasing number of bonded joints, explains Ricca. "This makes a reliable and cost efficient quality check an even more important factor in maintaining high quality and production rates. The automatic quality check using the FLIR A615 thermal imaging camera makes that possible."