What is condition monitoring? A beginner’s guide to preventative maintenance
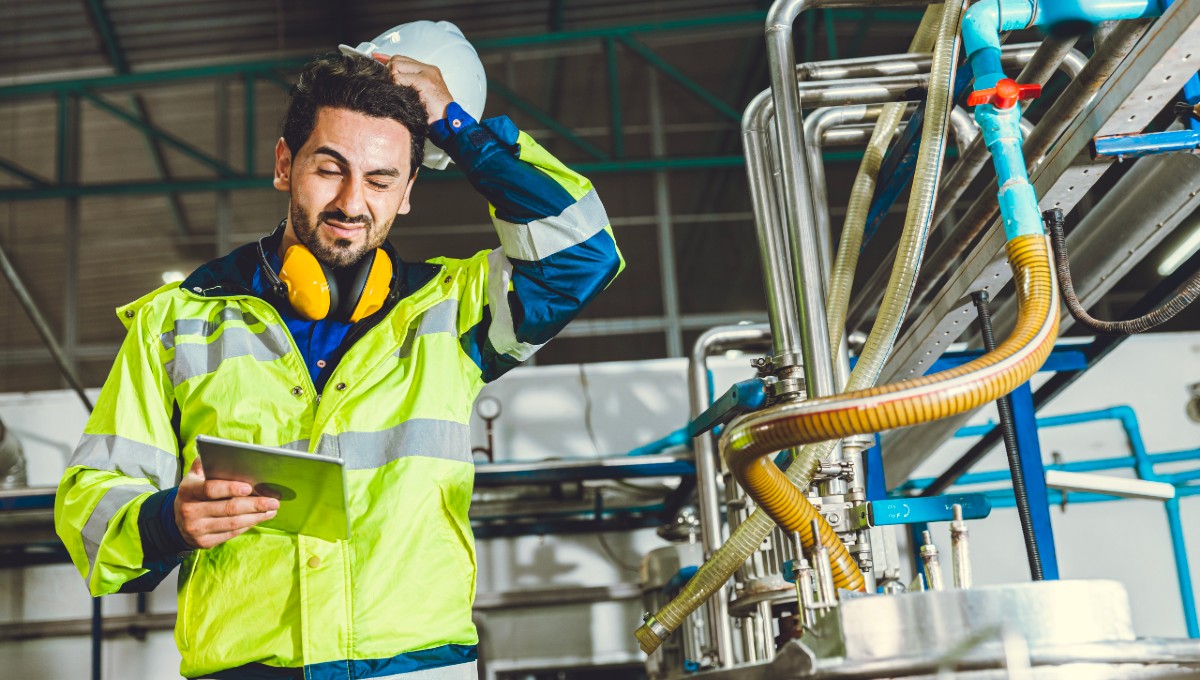
The term ‘condition monitoring’ is everywhere in the global manufacturing and engineering sectors - but what does it mean?
The clue is in the name; ‘condition monitoring’ is essentially monitoring the condition of industrial components through regular inspections to predict long-term degradation and failure. In fact, it can reduce breakdowns by a staggering 70% and lower maintenance costs by as much as a quarter.
Also called preventative maintenance, it allows operators to catch issues early, plan repairs in advance and avoid unnecessary downtime - ultimately boosting productivity by as much as 25%.
That old adage of prevention being better than the cure still rings true - effective condition monitoring can prevent downtime, keep repair costs down and ensure operating costs stay competitive.
But how can companies make condition monitoring work for them?
Bottom-line benefits of condition monitoring
Instead of working machines to failure, which can be costly in both expenses and losses due to unplanned downtime, incorporating a dedicated schedule of condition monitoring can actively yield a host of benefits that boost both your productivity and your bottom line.
These include:
- Extending the lifespan of machines, motors, and systems
- Reducing energy expenses
- Avoiding unplanned outages and unexpected downtime
- Drastically cutting the time needed for maintenance
- Optimizing maintenance programs
- Improving asset management decisions
FLIR has a range of high-performance tools to map degradation and identify patterns in equipment use to help operators detect problems before they can worsen.
A powerful proposition: how to use condition monitoring
Preventative maintenance is no, a one-size-fits-all process. It typically inspects individual components or functions in detail - these can be anything from inspecting the vibrational frequency of industrial equipment to the temperature of components, and even the energy used or lost by these components.
Monitoring this with pinpoint precision allows for companies to uncover trends and reveal which elements of their operation are wearing faster than others so that they can arrange targeted repairs. It allows efficacy improvements to drive up yield and drive down power consumption - and other escalating costs.
Key applications for condition monitoring
Any industrial environment can incorporate condition monitoring into its maintenance routine in order to get the benefits.
If a component wears, it is susceptible to performance degradation. This is especially true when it comes to mechanical elements that move - such as rotating machinery, compressors, pumps or motors - or electrical elements that are in high-demand.
Condition monitoring is especially useful for identifying and analysing:
- Vibrations
- Stress waves (which can lead to cracks and other faults)
- Temperature
- Electrical signals
From acute thermography through to spark-proof cameras for potentially explosive environments and acoustic imaging to detect air leaks in compressed air systems as well as inspection software, there is a FLIR technology to suit virtually every inspection need.
For inspecting the temperature of elements around your facility, hand-held thermal imaging systems can yield sizable savings. For static elements, a fixed thermal camera system can offer similar benefits.
For electrical components, measuring currents, and quality assurance testing, FLIR also has a robust range of test and measurement tools. For detecting gas, air leaks or partial discharge in your machinery components or production line, explore FLIR’s range of gas detection cameras or acoustic imaging cameras.
What’s more, your insight isn’t limited to your device; FLIR’s intuitive software takes predictive maintenance a step further, enabling impactful analysis of even the most demanding datasets. To explore the operational improvements that FLIR Thermal Studio can offer your condition monitoring routine, click here.
If you’re concerned about energy loss, system inefficiencies, extensive downtime or other issues driving your costs up and productivity down, get in touch with our team of condition monitoring specialists today.