Leaders of the Steel Industry use FLIR GF346 Gas Detection Cameras to Detect Harmful Carbon Monoxide Gas
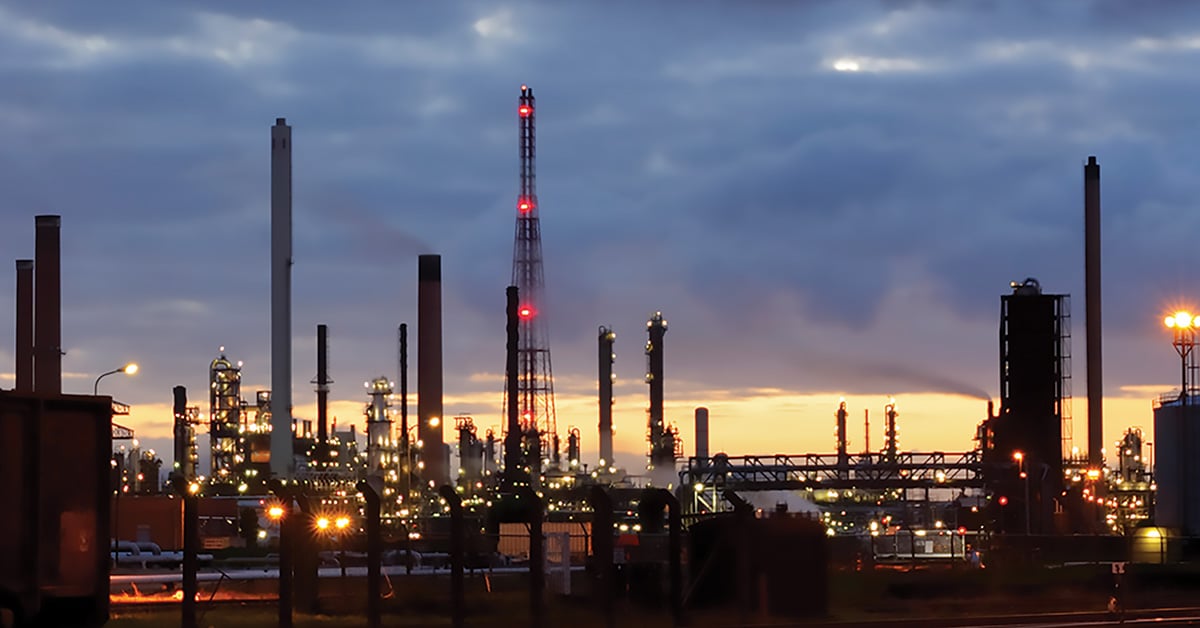
Many steel companies have similar challenges tied to safety, productivity and environmental stewardship. They have the capacity to produce dozens of tonnes of crude steel annually, host operations in multiple countries, and employ tens of thousands of people—all of which can prove an challenge to safely producing hot and cold rolled coils, sheets, galvanized sheets, tubes, wire rods, construction rebars, and bearings.
WORKER SAFETY IN THE STEEL INDUSTRY & CONSERVING CARBON MONOXIDE
Ensuring environmental responsibility and worker safety in all production units is a top priority for steel companies of all sizes. These facilities use blast furnace, coke oven, and Linz-Donawitz (LD) gases in the production process, the primary component of which is carbon monoxide (CO). CO is not only harmful to the environment: it can be life-threatening to workers.
In most plants the gases created in the production process are reused for power generation and reheating furnaces, which means that a CO leak could carry a devastating cost to the company in terms of money and energy. In addition to ensuring safe and efficient operations, many steel companies are also choosing to be environmentally responsible in their processes which is proven in some of their Environmental, Social and Governance (ESG) programs.
Image of a carbon monoxide (CO) leak in normal mode (top) and high sensitivity mode (bottom) from a blast furnace during normal operation.
TRIED AND TESTED TECHNOLOGY THAT DETECTS GAS LEAKS
Gases are invisible to the naked eye and the effect of leaks is often very gradual, so identifying the source of a carbon monoxide gas leak can be difficult. The leaks can be masked by changes in airflow, making fugitive gases challenging to detect when using more traditional methods. In an effort to find a better solution, steel operators have a unique solution to consider: an optical gas imaging (OGI) camera. While optical gas imaging is not widely used in the steel industry, it is a foundation of leak detection and repair (LDAR) technology used in a variety of other industries. The utility industry uses specialized OGI cameras to detect sulfur hexafluoride (SF6) gas leaks in substations and other areas within the electrical transmission supply chain. In the oil and gas industry, where OGI was first utilized, this technology is commonly used for the detection of hydrocarbons and VOC gases throughout the entire supply chain. OGI is approved by the U.S. EPA as an alternative work practice and even designated as the best system for emissions reduction (BSER) for regulations in the oil and natural gas sectors. Companies such as Statoil, BP, Chevron and ExxonMobil all use OGI cameras to detect gas leaks.
CO pipeline leak identified with a FLIR GF346 optical gas imaging camera.
The FLIR GF346 uses a specially filtered thermal detector to visualize CO and other harmful gases. The camera can be used to quickly scan for gas across wide areas and from a safe distance, without interrupting a plant’s production process. CO emissions can be a significant threat to steel manufacturing operations so emissions need to be closely watched. Even the slightest leak in a vent stack or pipe can have a devastating effect. The FLIR GF346 scans potential leak points rapidly from a distance and allows the user to pinpoint their source in real time. By ensuring there is sufficient Delta T (temperature difference between the ambient temperature at the leaking component and the background scene) technicians can achieve the optimal image contrast needed to detect the lowest level of gas emissions using the GF346’s high sensitivity mode.
REAL WORLD EXAMPLES OF OPTICAL GAS IMAGING IN THE STEEL INDUSTRY
A primary use for the FLIR GF346 is finding elusive leaks near the casting floor. Often, technicians are unable to detect the CO gas leak source in the casting floor area. Leaks occasionally begin in the late evening hours, so a lack of sunlight and the frequent change in natural airflow direction make it difficult to trace the source of leakage. With the help of a FLIR GF346 optical gas imaging camera, inspectors can scan all possible sources of the leakage point near gas piping both inside and outside the steel-making units.
CO leak from a bleeder valve detected with the FLIR GF346 camera.
The GF346 can find leaks in a variety of scenarios which can be up to 60 meters away from the casting floor. Gas can escape from a flange joint in a line that supplies gas to the hot strip mill reheating furnace from the gas mixing station. One remedy would be to close off and secure the area and communicate the findings for immediate corrective action, preventing an unsafe incident and closing off the source of the leak.
In addition to casting applications, there are extensive pipelines within steel production facilities with the potential for dangerous leaks. For example, during typical LDAR scans a user may not always find a leak in the steel making unit but can expand their inspection to gas lines outside the main facility premises. In these situations, the FLIR GF346 can detect leaks from main CO gas lines at a variety of points that supply gas to the hot strip mill furnace from gas mixing stations, like flange joints. As a result, a facility can develop a routine program to do pipeline scanning on a consistent basis. Using the GF346 to inspect connections, joints and other potential leak points provides an efficient way to further improve safety within a broader facility footprint and reduce emissions helping the organization meet environmental stewardship metrics.
Steel industry operators can use the FLIR GF346 to inspect blast furnaces, which produce liquid iron for steel making. Blast furnaces have tuyers for supplying hot blast to the furnace that are fitted to the furnace shell. Frequent leakage of CO gas from these tuyers creates an unsafe and unhealthy atmosphere at the tuyer platform and above. Inspectors can use the GF346 to scan all tuyers and identify the leaky tuyers from a safe distance. If a leak is discovered, operators can take immediate corrective action and update the tuyers with a new welded design. After changing the tuyers, a user can scan the area with the GF346 again to confirm the leaks were eliminated. As a result, operating personnel are now working in a safe, gas-free environment.
CO vent stack leak at a steel plant.
Hot strip mill applications produce hot-rolled sheets for automobile and LPG grades. Mills are fed by reheating furnaces which use carbon monoxide-rich blast furnace gas and coke oven gas as fuel. Leakage of unburnt CO can be identified through the camera, and inspectors can quickly and safely find the source of the leak(s) in pipe joints. Once a leak is found, a technician can take immediate corrective action to eliminate the presence of CO near the furnace.
TIME IS MONEY
A key advantage in using a FLIR GF346 for LDAR inspections is the high Return on Investment of the technology. Gas leaks can cost money in a variety of ways: lost product, added safety expenses, and increased downtime. Using an OGI camera for LDAR inspections can help the steel industry streamline their shutdown processes and procedures. These shutdowns can cost a company a considerable amount of money; an OGI camera like the FLIR GF346 can show operators exactly what needs to be repaired, allowing maintenance teams to plan for repairs and avoid unexpected shutdowns. There is a safety element as well: adding a telescopic lens to the FLIR GF346 allows operators to look for dangerous leaks from a safe distance, keeping them out of confined/hot work permit areas. The FLIR GF346 can also reduce downtime by allowing operators to identify areas of interest during regular operations, and then schedule closer inspections for planned shut downs. Since a turnaround could run 24/7 with hundreds of personnel working 24 hours a day, the time spent looking for leaks without the benefit of an OGI camera can be considerable. Saving even an hour of laborious inspection time would help pay for the camera.
The FLIR GF346 OGI camera can serve as an extremely important tool for steel companies, helping inspection crews identify problems before they become catastrophic and conducting surveys without shutting down operations. The GF346 is ideal for monitoring plants where it is difficult to reach components with handheld contact measurement tools such as gas sniffers, or TVAs. Inspectors can scan thousands of components per shift without the need to interrupt the process. Optical gas imaging cameras also allow operators to detect profuse leaks and find their source while working from a safe distance, outside the gas cloud. Using the FLIR GF346, steel companies can improve work safety, reduce environmental impact, and help them maintain regulatory compliance while increasing efficiency as this technology can operate without interrupting a plant’s production process.